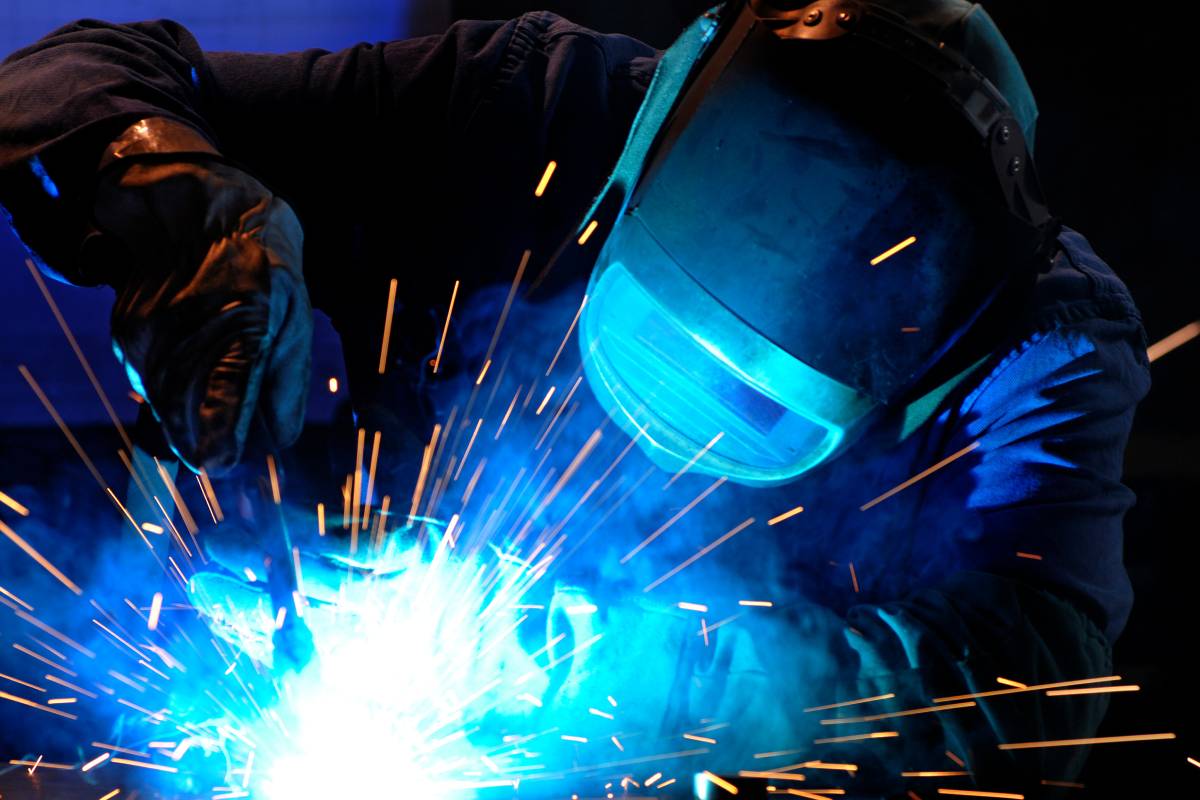
10 Sep Why Is It Important to Wrap Welds?
Attention to detail in welding is critical. It’s the best way to create solid and durable joints, prevent failures or corrosion, enhance safety, and achieve a high-quality, professional finish. Also, it’s good to know that the I.B. Moore Manufacturing team takes all its manufacturing processes very seriously, one step at a time. Welding is one of our core competencies, and our experts are happy to discuss finer points like wrapping corners in welding.
What Does Wrapping Corners in Welding Mean?
Welders join materials, usually metals, by melting and fusing them using heat, pressure, or both. “Wapping corners” is a method that ensures a weld doesn’t terminate abruptly at an edge. Instead, the bead continues around the edge for a uniform, continuous weld across the connected surfaces. It’s a common practice in projects where welded joints must endure stress or load. Examples include fabricating heavy machinery, automotive components, or metal furniture.
When you wrap corners, welding is more effective. The metal is less likely to experience weak points or areas vulnerable to cracking. This technique spreads the stress load evenly across the welded joint, reducing the chance of failure. It also prevents corrosion by eliminating gaps or crevices where moisture or contaminants might accumulate.
Why Wrap Corners? Welding Strength and Durability
Welding involves joining two pieces of metal but can create potential weak spots along a seam. A weld that stops suddenly at an edge can concentrate stress at that point, leading to fragility over time. By wrapping the weld around corners, the stress distribution becomes more uniform, reducing the risk of failure.
Wrapping corners during welding also prevents cracking, essential for parts exposed to repeated stress or impact. A continuous weld is less likely to fail than one with a sharp endpoint since it doesn’t present a single point of weakness. That’s important in structures that must withstand dynamic forces, like those in construction, transportation, and industrial applications.
Wrapping Corners in Welding Prevents Corrosion and Extends the Lifespan
Welds that stop abruptly at corners can create small crevices where water, chemicals, or other corrosive elements could gather. Over time, those spaces can cause rust and material degradation. Wrapping corners in welding eliminates crevices, making it harder for moisture or contaminants to attack a welded joint.
Wrap Corners in Welding for Better Aesthetics
Wrapping corners in welding also looks better. A continuous weld bead around the edges creates a cleaner, more polished look, a huge plus in visible metalwork, like railings, gates, or furniture. Simply put, a well-executed corner wrap looks more professional.
Reduced Maintenance Needs
A continuous weld reduces the chances of wear and tear caused by environmental factors, vibrations, or physical impacts. This lower rate of deterioration means less frequent repairs or replacements are needed, saving time and resources in the long run.
Wrapping Corners in Welding: How I.B. Moore Does It
I.B. Moore offers products and services that align with best practices, including wrapping corners in welding. With decades of experience in. rubber and custom fabrications, we’re well-equipped to provide materials that complement effective welding techniques for the highest quality and longevity in our industrial projects.
I.B. Moore Fabrication Solutions
I.B. Moore provides solutions tailored to specific welding needs for projects that require customized fabrication. From supplying durable rubber materials that work alongside metal components to fabricating specialized gaskets and seals, our materials and best practices support the structural integrity of welded joints.
Our expertise extends to using and supplying materials that prevent corrosion. Our rubber linings and protective coatings extend the life of welds and reduce maintenance costs.
Products That Protect Welds
I.B. Moore’s rubber gaskets and seals protect welded joints from environmental damage, keeping out moisture and contaminants from the welded area. These products are available in various sizes and configurations, providing flexible options for projects of any scope or scale.
Whether you’re involved in manufacturing, construction, or any industry that relies on metal components, wrapping welds is an essential technique for strength and resilience. I.B. Moore offers the materials and expertise to support effective welding practices with tailored solutions that meet your business’s unique needs.
Work With I.B. Moore for Your Next Project
At I.B. Moore Company, LLC, we understand the importance of quality welding and the role of supporting materials in creating durable, reliable connections. Contact us in Lexington, KY, and we’ll explain how our high-quality products and services will make a difference in your next welding project.