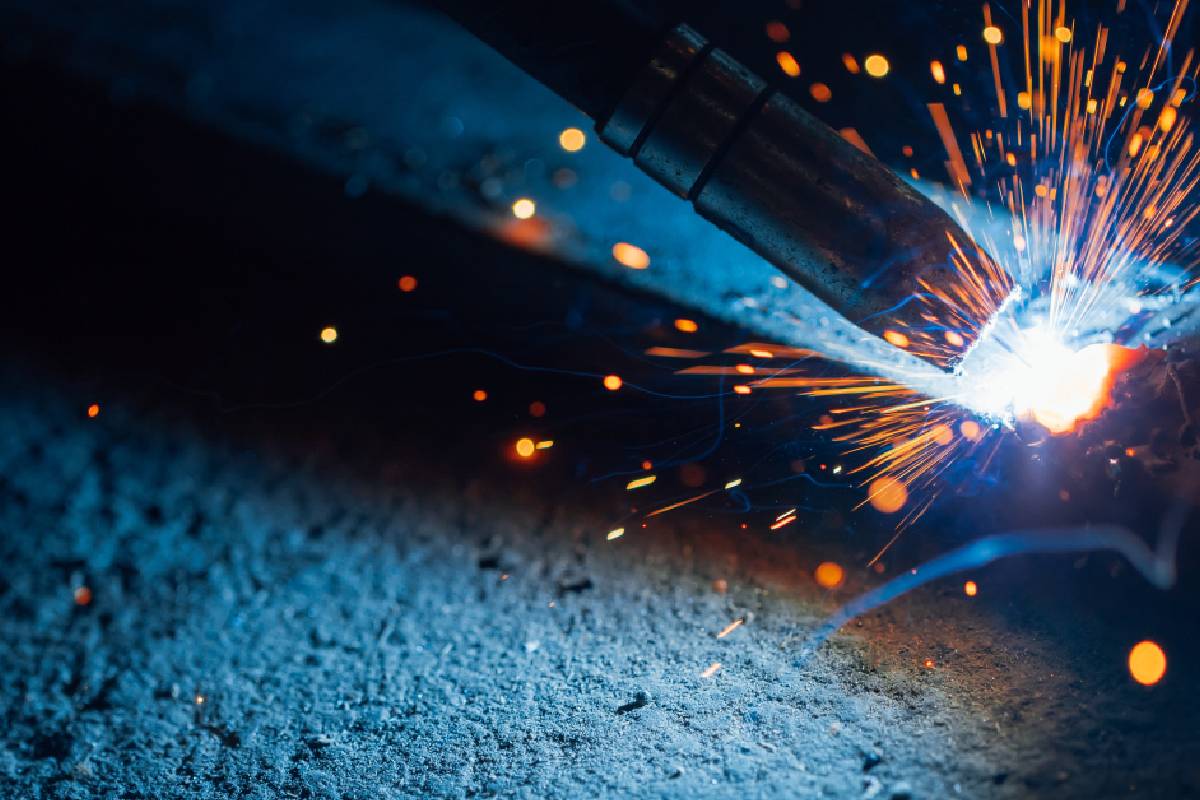
06 May How To Tell The Difference Between Good Welds and Bad Welds
Welding is a critical process for many industries, like construction and manufacturing. It’s a
process of joining metals together by melting and fusing them. It involves heating the materials to a high temperature, often using an electric arc or flame, and then applying pressure to create a strong bond.
Welding fabricates structures, repairs components, and creates intricate designs. It plays a vital role in building infrastructure, producing machinery, and crafting everyday objects. The process enables the fabrication of durable, reliable, and complex metal assemblies essential for modern society.
Whether you’re a professional welder or someone assessing the quality of welded products, distinguishing between good and bad welds is essential. It can save time and money and also prevent safety hazards. So, how can you tell when a welder has done quality welds? Good or bad, here’s how to tell the difference.
Welds: Good and Bad – Understanding the Basics
Recognizing Good Welds
Good welds exhibit several noticeable characteristics that signify quality craftsmanship and structural integrity. First, they have a consistent bead appearance, with uniform width and smooth transitions between weld passes. A good weld should also penetrate the base metals adequately, ensuring a solid bond that can withstand stress and pressure. Additionally, good welds are free from defects such as cracks, porosity, or excessive spatter.
Identifying Bad Welds
Bad welds display noticeable flaws that compromise their strength and durability. These flaws may include uneven bead formation, incomplete penetration, or excessive spatter. Bad welds often have defects like irregular bead shapes, cracks, porosity, or undercutting. Those can weaken the weld joint and increase the risk of failure.
Key Characteristics to Look For When Comparing Good Welds vs. Bad Welds
Penetration refers to how deeply the weld filler material has fused with the base metals. The filler material penetrates the base metals sufficiently in good welds, creating a strong bond between the joint surfaces. In contrast, inadequate penetration in bad welds makes weak joints susceptible to separation under load or stress.
Inspecting for defects is essential when assessing weld quality. Good welds are typically free from defects like cracks, porosity, or undercutting. These imperfections can compromise the structural integrity of the weld joint, leading to premature failure or performance issues. Regular inspection and quality control measures are necessary to detect and correct defects in welded components.
How Can I Evaluate Weld Quality?
Visual inspection is one of the simplest yet most effective methods for evaluating weld quality. Take the time to examine the weld bead closely, looking for irregularities or signs of defects. Then, compare the weld against accepted quality standards to determine its suitability for the intended application.
Nondestructive testing techniques, such as ultrasonic testing or radiographic inspection, can provide valuable insights into weld integrity without compromising the structure. These methods allow you to detect internal defects or other issues that may not be visible to the naked eye, ensuring a thorough quality assessment.
When in doubt, seek guidance from experienced welders, engineers, or inspectors who can offer expertise and advice on assessing weld quality. Their insights can help you identify potential issues and implement solutions to improve welding processes and outcomes.
What Should I Do When I See a Bad Weld?
When encountering a bad weld, address it promptly. Halt any associated operations to prevent potential hazards. Notify relevant personnel, such as supervisors or welders, detailing the issue. Document the weld with photos or notes for further analysis. Finally, you must take proper corrective action to maintain safety and quality standards and follow up to ensure the resolution of the problem.
At I.B. Moore, our team of experts thrives on tackling challenges with strategic ingenuity, crafting custom solutions for every industrial rubber need. We pride ourselves on offering diverse products with compounds and materials to match each customer’s unique application demands.
Leveraging our extensive network of global partnerships, we ensure access to multiple avenues for sourcing our top-quality products. We also know a few things about welding.
Contact Us for Tailored Industrial Solutions
As a company specializing in industrial rubber products, I.B. Moore is a manufacturer, fabricator, and distributor. We prioritize prompt customer assistance by delivering tailored solutions for various industrial needs. Our extensive technical knowledge, dedication to top-notch quality, and consistent reliability reduce downtime for our clients.
We are the trusted choice for businesses that aim to maintain the safety and reliability of their equipment. Contact us in Lexington, Kentucky, for nationwide service.