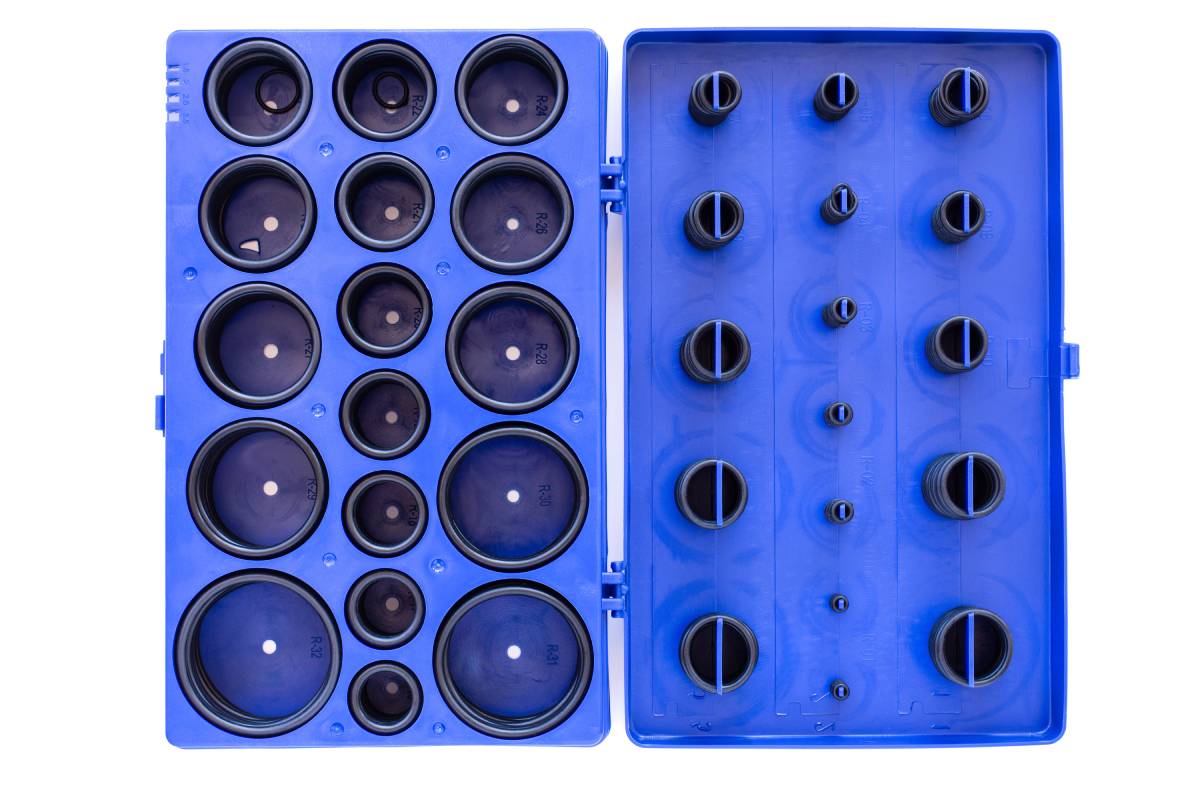
07 Jul What is NBR (Nitrile Rubber)?
Nitrile rubber is a highly versatile synthetic elastomer used in modern manufacturing. This synthetic rubber, commonly abbreviated as NBR and called Buna-N, combines two chemicals: butadiene and acrylonitrile. The resulting flexible material is exceptionally resistant to oils, fuels, many chemicals, and different temperature ranges.
I.B. Moore Manufacturing uses nitrile rubber for O-rings, seals, custom-molded products, and gaskets. It’s one of the many materials we offer, and NBR is the best choice for specific applications.
What Industries Use NBR?
Automotive manufacturers rely heavily on NBR for critical fuel system components. Fuel hoses, gaskets, and seals made from nitrile rubber resist degradation from gasoline, diesel, and other automotive fuels. We carefully consider fuel composition and operating temperatures when recommending these components and select the appropriate acrylonitrile content.
NBR seals and O-rings benefit hydraulic systems across various industries. The material’s excellent compatibility with mineral-based hydraulic oils and synthetic fluids prevents system contamination and effectively maintains pressure integrity. For maximum performance, we account for dynamic versus static applications, as movement affects wear patterns and seal geometry requirements.
FDA-approved grades of nitrile rubber enhance food processing equipment as well. These specialized formulations meet strict safety standards and offer dependable chemical resistance against cleaning agents and food-grade oils. White or clear NBR compounds help with visual inspection during maintenance procedures.
Oil and Chemical Resistance Guidelines
NBR’s petroleum resistance depends on the specific oil or fuel involved. Aromatic hydrocarbons like benzene and toluene cause more swelling than other compounds. For these applications, we consult compatibility charts and conduct extensive material testing.
Nitrile rubber also resists many acids, bases, and solvents. However, it has poor resistance to ozone, strong acids, and polar solvents like acetone or methyl ethyl ketone. Temperature effects on NBR’s chemical resistance also mandate careful consideration: Higher temperatures generally increase the rate of chemical attack, while lower temperatures may cause embrittlement in some NBR formulations.
NBR Temperature Tolerances for Different Applications
Cold-weather applications demand meticulous selection of proper NBR acrylonitrile content levels. Lower percentages maintain excellent flexibility at subzero temperatures, so they’re particularly suitable for outdoor equipment and cold storage facilities. However, this approach can significantly reduce oil resistance capabilities.
We strongly recommend specialized NBR compounds with enhanced thermal stability for demanding high-temperature applications. These formulations resist hardening and cracking, even at consistently elevated temperatures; heat-resistant grades suit engine compartments, industrial ovens, and hot oil systems.
Thermal cycling severely impacts NBR components over time. Repeated heating and cooling cause stress cracking when material selection doesn’t account for expansion and contraction rates. We strategically leverage groove design and material choice to counteract those effects effectively.
Three More NBR Selection Tips
Hardness selection also impacts NBR performance characteristics. Softer compounds (60-70 Shore A) offer better sealing at low pressures but may extrude under high-pressure conditions. Harder compounds (80-90 Shore A) resist that effect.
Your compound selection should reflect the total operating environment, not just primary exposure conditions. Secondary factors like intermittent chemical contact, cleaning procedures, and storage conditions all influence NBR durability.
Our testing protocols will validate your material choices before full-scale implementation. Ask us about accelerated aging tests, chemical immersion studies, and mechanical property evaluations.
What Material Can I Use When NBR Isn’t Appropriate?
When nitrile rubber isn’t the right choice, we might recommend one of these alternatives:
- Silicone rubber handles extreme temperatures better than NBR. Because it’s food-safe and flexible, it’s commonly used in kitchen bakeware and medical devices.
- EPDM rubber resists weathering, ozone, and UV rays that would damage NBR. You’ll find it in car door seals and roofing materials.
- Fluorocarbon rubber (Viton) costs more, but it’s essential for chemical plants and aerospace applications. It stands up to harsh chemicals that would destroy other rubbers.
- Natural rubber provides excellent flexibility and strength for general purposes like tires and gloves but doesn’t resist oils.
The key is matching the material’s strengths to your application’s needs: temperature, chemicals, movement, weather exposure, and flexibility.
We Can Specify NBR for Your Next Project
I.B. Moore Manufacturing has proven expertise in nitrile rubber applications that tackle application challenges. Our technical team will help you select the right NBR compound for your requirements for maximum performance and cost-effectiveness. Contact us today to discuss your project and get a free quote. We’re based in Lexington, KY, and provide nationwide service.