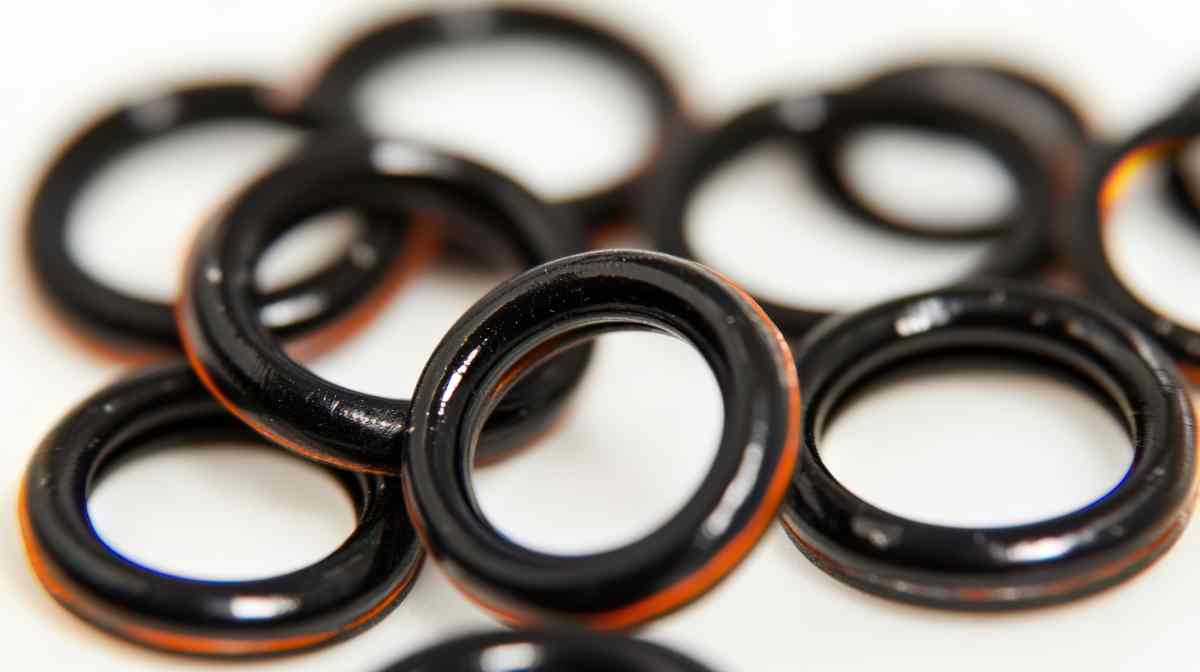
17 Mar What Are The Standards for O-Rings
Manufacturing industries have standards for very good reasons: product safety, quality, and compatibility across different brands, for instance. These guidelines promote efficiency, reduce costs, and create customer confidence. They also encourage innovation, create level playing fields, and promote accessibility.
At I.B. Moore Manufacturing, we apply gasket industry standards to our O-ring fabrication and other products. Various industries, such as aerospace, automotive, medical, and manufacturing, use O-rings in sealing applications and turn to us for custom and pre-fabricated versions. These small but essential components prevent fluid and gas leakage by creating secure seals between mating surfaces.
International standards define the specifications for O-rings to maintain consistency, compatibility, and reliability. The International Organization for Standardization (ISO) is the most recognized organization that sets these guidelines; manufacturers, engineers, and designers must understand and follow them.
The Importance of ISO O-Ring Standards
ISO standards for O-rings establish guidelines for material properties, sizing, tolerances, and performance characteristics. These standards help manufacturers produce consistent products that are compatible across different systems and industries. One of the most widely referenced standards is ISO 3601, which defines the general dimensions, tolerances, and quality acceptance criteria for O-rings.
ISO 3601 classifies O-rings into two primary categories:
- ISO 3601-1: This category applies to general-purpose O-rings used in standard sealing applications.
- ISO 3601-3: This classification covers O-rings for high-integrity sealing applications requiring enhanced reliability.
Since it categorizes O-rings by application needs, ISO 3601 helps engineers choose the appropriate seal for their specific operating conditions. This standard also outlines permissible defects and quality acceptance levels, reducing premature failure risk and improving reliability.
Standard O-Ring Measurements and Tolerances
ISO 3601 defines O-ring sizes using three parameters:
- Inside Diameter (ID): The internal circumference of the O-ring.
- Cross-Sectional Diameter (CS): The thickness of the O-ring material.
- Tolerance Levels: Acceptable dimensional variations for a secure fit and effective sealing performance.
ISO 3601 specifies five tolerance classes, ranging from Class A (tightest tolerances) to Class E (widest tolerances). The selection of a tolerance class depends on the application’s requirements, like operating pressure, temperature fluctuations, and chemical exposure. While tighter tolerances enhance sealing performance, they might require higher precision during installation.
How ISO Defines O-Ring Sizes
The ISO 3601 also standardizes O-ring sizes for global consistency, with metric and inch-based measurements. Metric sizes are most commonly used in European markets, and inch-based sizes align with United States standards and other regions. ISO 3601-1 further categorizes O-ring sizes into G-series for general industrial applications and A-series for aerospace and high-performance applications.
It’s Not Only About Size and Tolerance
Selecting the correct O-ring goes beyond choosing the right size and tolerance. ISO standards also specify guidelines for material composition and hardness (durometer). Those standards apply to the O-ring’s ability to withstand environmental conditions, mechanical stress, and chemical exposure.
Material Selection
Different materials offer unique O-ring properties suited for specific applications. Some of the most commonly used materials include:
- Nitrile (NBR): Resistant to oil and fuel. Ideal for automotive and industrial applications.
- Silicone (VMQ): Flexibility at extreme temperatures. Suited for medical and food-grade applications.
- Ethylene Propylene Diene Monomer (EPDM): Resistant to weathering, ozone, and water-based solutions. Commonly used in outdoor and water-processing applications.
- Viton (FKM): Known for superior resistance to heat, chemicals, and fuels. Used in aerospace, automotive, and chemical processing applications.
- Polytetrafluoroethylene (PTFE): Exceptional chemical resistance, low friction, and high-temperature stability. Suitable for seals, gaskets, and non-stick applications.
- Styrene-Butadiene Rubber (SBR): Provides good abrasion resistance and durability. Used in car tires, conveyor belts, and industrial seals.
These ISO material specifications help engineers ensure the longevity and reliability of O-rings in various environments.
Surface Finish Considerations
O-ring surface finishes also play vital roles in sealing efficiency. A smooth, defect-free surface allows better contact with mating surfaces, minimizing the risk of leaks. ISO standards outline acceptable surface imperfections and recommended finishes to optimize performance in demanding conditions.
O-Ring Quality Control and Acceptance Standards
Finally, ISO 3601 also establishes quality control standards for consistency. These standards define acceptable defect levels so O-rings meet performance requirements before use.
This is a step-by-step, thorough process. First, manufacturers assess O-rings for surface imperfections, irregularities, or deformities. Then, the O-rings are precisely measured to confirm compliance with ISO-defined standards. The seals are also subjected to pressure, temperature, and chemical exposure simulations to verify durability.
Strict adherence to these quality control measures means that O-rings will perform reliably in their intended applications.
Contact I.B. Moore Manufacturing for Reliable O-Ring Solutions
I.B. Moore Manufacturing provides high-quality O-rings that meet international specifications and our highest standards. Our talented staff can help you select the best O-rings for your application, with exceptional customer service throughout the process. Contact our Lexington, KY, team of experts for nationwide service.