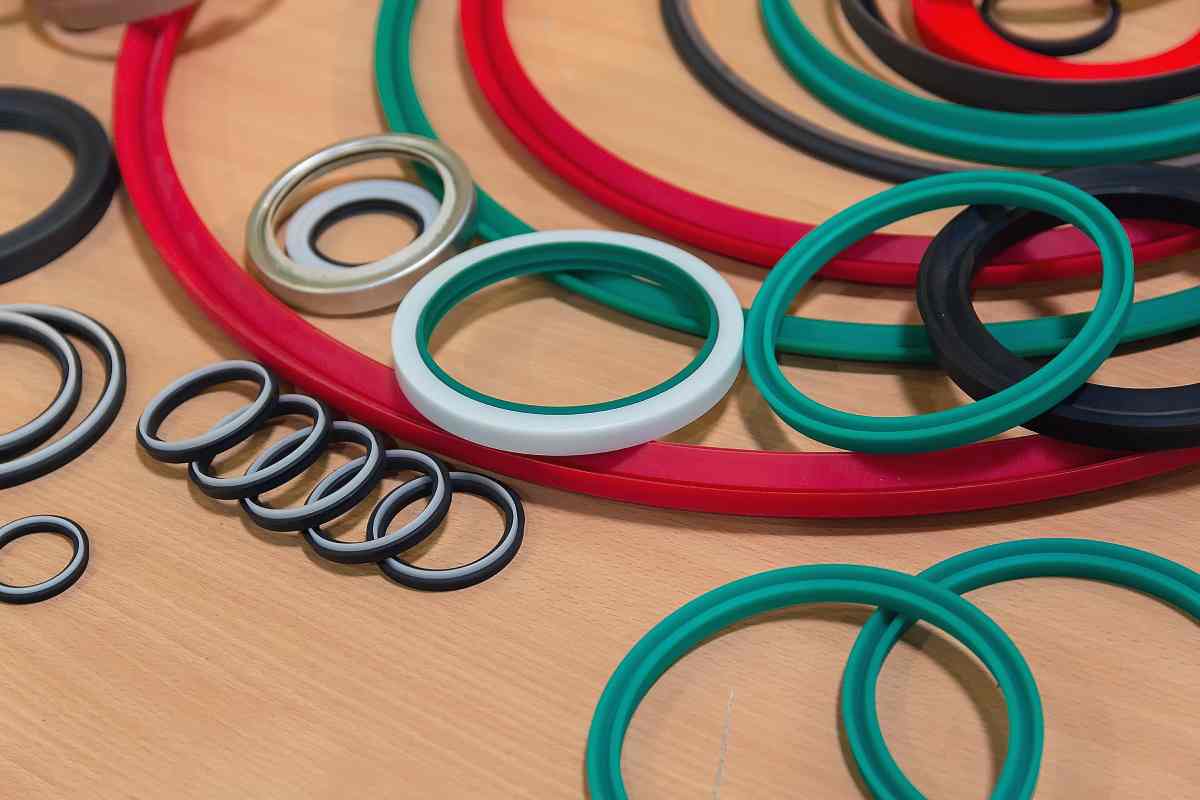
20 Jan The Benefits of Custom Sealing for Industrial Uses
Custom seals are specialized components that create tight, leak-proof barriers in machinery, equipment, and industrial systems. They prevent fluids, gases, or contaminants from leaking for better efficiency and performance. Unlike mass-produced, standard seals that fit common applications, we design custom seals for particular systems or processes.
Our custom sealing design and fabrication teams consider a seal’s size, shape, material, performance requirements, and exposure to environmental conditions as part of the parameters of success for each of our clients. These seals offer many advantages, including the ones below.
The Benefits of Custom Sealing Solutions
These benefits are building blocks for long-term durability, reliability, and success:
Perfect Fit for Specific Applications
Standard sealing solutions fit a broad range of applications but may not always provide the best fit for every project. Custom sealing solutions match the exact dimensions and requirements of the application. That ensures a more reliable seal and prevents the risks associated with improper fit: leakage, contamination, and equipment failure.
Improved Durability
In industrial settings, machinery and equipment face extreme conditions that can lead to wear and tear over time. We make custom sealing solutions from specialized materials that are better suited to these challenging conditions. For example, seals designed for high temperatures or aggressive chemicals last longer when made with the correct materials. Custom seals can also be designed with additional reinforcement to maintain their integrity over time.
Cost-Effective Long-Term Solution
Although custom sealing solutions may involve higher initial costs compared to standard products, they often result in significant savings over the long run. By providing a better seal, they reduce the likelihood of frequent replacements, downtime, and maintenance costs. Additionally, a well-designed custom seal optimizes machinery performance, increasing overall productivity and reducing the chance of costly failures.
Enhanced Efficiency and Performance
Through highly tailored designs, we create seals that maximize efficiency and minimize energy loss. That can contribute to more efficient systems, less energy consumption, and lower operating costs. Our sealing solutions also last longer.
Increased Safety
Leaks and system malfunctions can pose serious risks, especially in industries dealing with hazardous materials, high pressures, or extreme temperatures. Custom sealing solutions lower those risks via better sealing capabilities and added system safety; they safeguard employees and equipment, keeping injuries, maintenance, and downtime at a minimum.
Flexibility for Unique Needs
Every industrial process presents challenges, and a one-size-fits-all approach to sealing may not always meet those needs. Flexible, custom sealing solutions address issues like non-standard system designs or unusual environmental conditions.
How to Measure an O-Ring for Commercial Use
This step-by-step guide explains how to measure different types of O-rings for commercial use:
One: Measure the O-Ring’s Inner Diameter (ID)
The inner diameter is the distance across the inside of the O-ring. To measure this, you will need a caliper or micrometer. Measure the O-ring’s inside edges to determine the diameter. Be careful about taking precise measurements since even slight deviations can affect the seal’s performance.
Two: Measure the O-Ring’s Outer Diameter (OD)
The outer diameter is the distance across the outside of the O-ring. Use a caliper to measure the O-ring from edge to edge. This measurement is just as important as the inner diameter, as it determines how the O-ring fits in its groove.
Three: Measure the Cross-Section or Thickness
The cross-sectional diameter (or thickness) refers to the O-ring’s width. Take this measurement at the widest point of the O-ring, which is usually the same as its thickness. Use a micrometer to get an accurate reading of the O-ring’s cross-section. This measurement ensures that the O-ring fits snugly into its groove without being tight or loose.
Four: Consider the Material Type
Different materials make O-rings, each suited for various environments and applications. When selecting a custom O-ring, consider temperature, pressure, and chemical exposure. The material used will impact its performance, so select one based on the specific needs of the industrial environment.
Five: Groove Dimensions
The O-ring must fit into its groove with the proper dimensions to ensure a tight seal. Measure the groove width and depth accurately, or the O-ring won’t fit correctly. I.B. Moore Manufacturing designs custom seals with specific groove sizes based on your requirements.
Get the Right Seal for Your Industry Today
Don’t settle for generic products if your industrial operations require high-quality sealing solutions. At I.B. Moore Manufacturing, we offer custom sealing solutions that meet our client’s specific needs and can do the same for your industrial application. Contact us in Lexington, KY, for nationwide service.