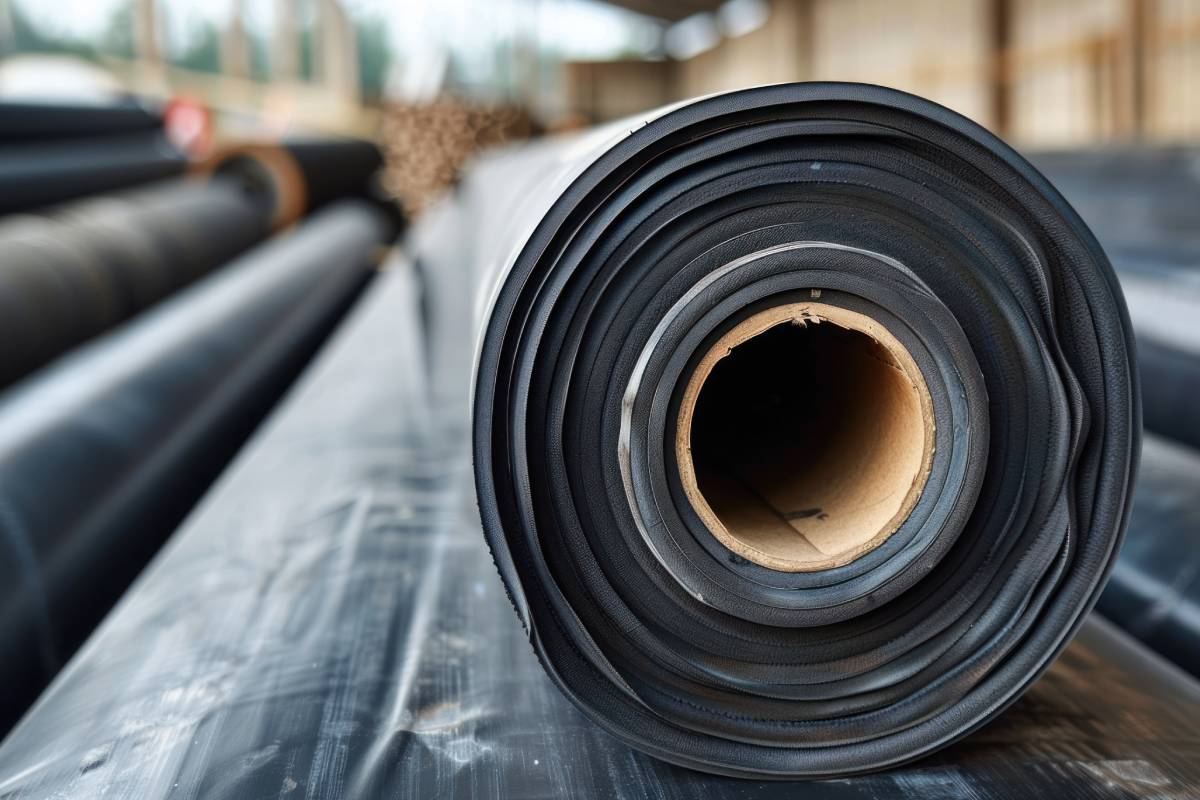
18 Jul What is EDPM Material and How is it Used in Applications
Ethylene Propylene Diene Monomer (EDPM) is a synthetic rubber made through polymerization. EDPM is known for its versatility and durability and is used in various industrial applications:
- Automotive: Seals, gaskets, hoses, and weatherstripping.
- Construction: Roofing membranes, window and door seals, and pond liners.
- Industrial: Conveyor belts, seals, and gaskets.
- Consumer Products: Appliance parts, electrical insulation, and garden hoses.
EPDM rubber is indispensable in demanding environments because of its exceptional weather resistance, UV stability, and longevity. The I.B. Moore Company team uses it to make industrial gaskets for its clients.
Understanding EDPM Material
EDPM rubber blends ethylene, propylene, and a diene monomer. It’s more durable than natural rubber and can withstand extreme temperatures, ranging from scorching summers to freezing winters. Its unique molecular structure also gives it excellent resistance to ozone and weathering.
How is EDPM Rubber Made?
- Monomer Selection: The process starts with choosing the building blocks:
-
- Ethylene (chemical compound)
- A diene monomer (chemical compound)
- Propylene (colorless gas)
- Polymerization Reaction: These monomers undergo a polymerization reaction, usually with a catalyst. This reaction creates long chains of EPDM rubber molecules.
- Polymer Chain Formation: Ethylene and propylene form the main backbone of the polymer chain, while the diene monomer creates cross-links between the chains, boosting the rubber’s elasticity and strength.
- Mixing and Compounding: The raw EPDM polymer has additives like fillers, oils, and curing agents. This mixture is compounded to achieve the desired properties for the final rubber product.
- Shaping and Molding: The compounded EPDM rubber is shaped and molded into the desired forms via extrusion, injection molding, or compression molding techniques.
- Vulcanization: The shaped rubber undergoes vulcanization, a curing process involving sulfur or other materials heating the rubber. This step creates more cross-links between the polymer chains, improving the rubber’s strength, elasticity, and durability.
Industrial EDPM Applications
In the automotive sector, industrial EDPM material is critical in sealing systems like door and window seals. Its ability to maintain flexibility and structural integrity under varying climatic conditions ensures consistent performance and a prolonged lifespan. EDPM is also resistant to automotive fluids and lubricants, making it a preferred choice for manufacturing gaskets and hoses.
EDPM rubber is in roofing membranes in the construction industry. These membranes provide needed waterproofing and weatherproofing solutions for protecting buildings against moisture and other environmental challenges.
Industrial EDPM material is a reliable insulator for cables and wires in electrical applications. It prevents electrical leakage, ensuring the safe transmission of power in various industrial settings. Its resistance to heat and chemicals makes it suitable for use in harsh environments where electrical components must perform consistently and safely.
How I.B. Moore Company Uses EDPM in Gaskets
Integrating EDPM rubber into designs involves leveraging its moldability and compatibility with different fabrication techniques. Processes like compression molding and extrusion enable the production of custom seals, gaskets, and profiles tailored to specific project requirements. Designers must also consider EDPM’s shrinkage rate and compression set values to optimize performance and ensure precise fits within assemblies.
I.B. Moore Company uses EDPM to fabricate industrial gaskets due to its exceptional properties that enhance sealing performance and longevity:
- EDPM’s excellent resistance to weathering, ozone, and UV exposure ensures gaskets maintain integrity in diverse environmental conditions, from extreme temperatures to outdoor elements.
- Its flexibility allows tight seals that prevent fluid and gas leakage, critical for operational efficiency and safety in industrial settings.
- EDPM’s compatibility with various fabrication techniques, such as compression molding and extrusion, enables us to produce custom gaskets for our clients.
EDPM Rubber and Environmental Sustainability
Beyond the benefits listed above, EDPM material aligns with sustainability objectives due to its recyclability and extended service life. Recycling initiatives within the industry contribute to minimizing waste and promoting eco-conscious manufacturing practices. By choosing EDPM for applications, I.B. Moore and our clients support environmental stewardship while upholding high-level performance and reliability standards.
EDPM rubber consistently delivers superior performance and enduring value. This material is preferred for businesses and designers seeking resilient solutions that endure environmental challenges and operational demands.
What is EPDM Material? I.B. Moore Company Has the Answers
For expert guidance on integrating EDPM material into your next project, visit I.B. Moore Company. With our specialized knowledge and commitment to quality, we provide tailored solutions that will exceed your expectations. For more information and nationwide service, contact us in Lexington, KY.