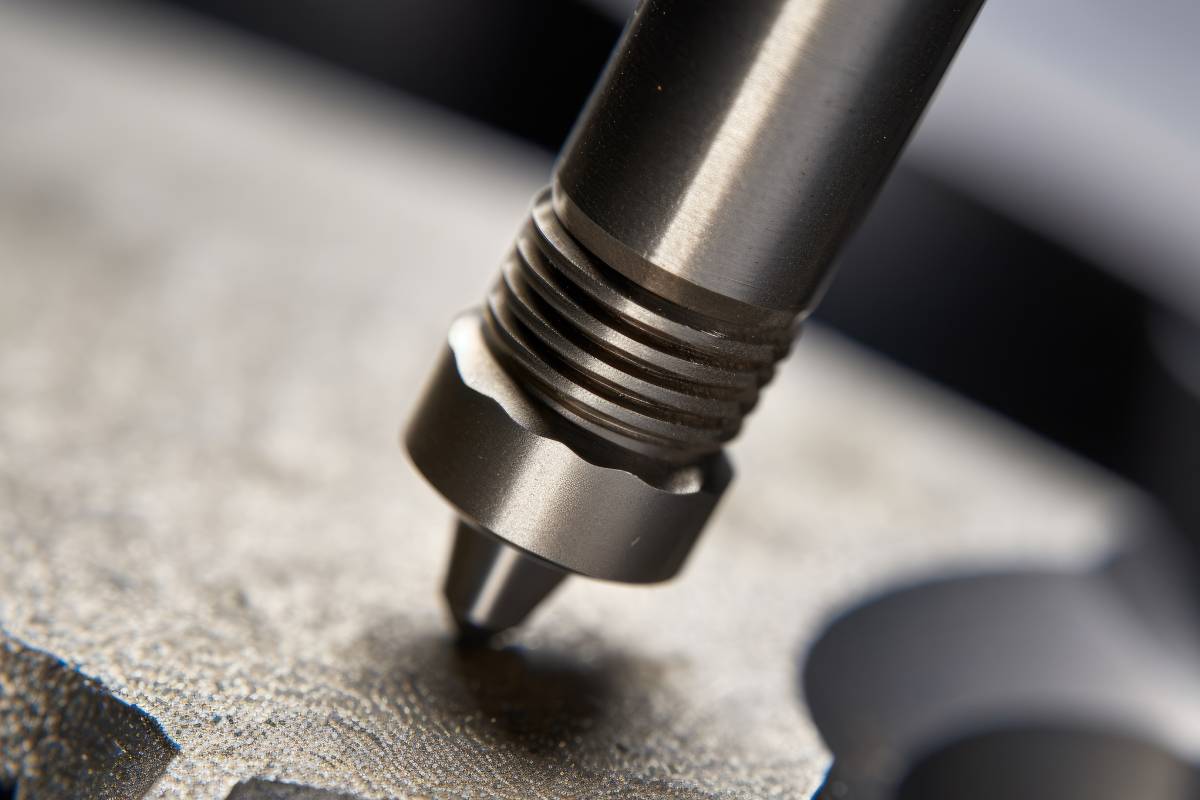
05 Jun What Is a Durometer and How To Use One
Understanding material properties is essential in many industries, especially when working with rubber, elastomers, and plastics. One fundamental property is hardness, and a tool frequently used to measure this is a durometer.
But what is a durometer, and how do you use one? The team members at I.B. Moore Company certainly know their way around this tool and are happy to explain what it is and how it works.
What Is a Durometer Part 1: Durometer Definition
A durometer is an instrument designed to measure the hardness of materials, specifically elastomers, rubber, and plastics. Hardness is a material’s resistance to indentation.
This tool consists of a calibrated spring and an indenter that presses into the material. The depth of the indentation shows the hardness level, which a digital screen displays. The term “durometer” refers to this specific type of hardness measurement tool.
Durometer Scale
The durometer scale quantifies resistance, with various scales specific to different materials and hardness ranges. The most common scales include Shore A and Shore D. Shore A is for softer materials like rubber, and Shore D is for more rigid plastics.
What is a Durometer Part 2: How to Use One
Durometer use is straightforward, but ensuring accurate readings requires attention to detail. Here’s a step-by-step guide:
- Prepare the Material: Ensure the sample is clean, flat, and at least 6 mm thick. If the material is thinner, stack layers to reach the required thickness.
- Select the Correct Scale: Choose the appropriate durometer scale for your material.
- Calibrate the Durometer: Check the calibration of your device before each use. That might involve using a reference block with a known hardness.
- Apply the Durometer: Place the durometer perpendicular to the material’s surface. Press the indenter into the material with consistent pressure, avoiding tilting or sideways movement.
- Read the Measurement: Hold the durometer in place for the recommended duration (usually 1-3 seconds) and then read the hardness value on the dial or digital display.
- Repeat as Necessary: Repeating the measurement at multiple points on the material ensures accuracy and accounts for any inconsistencies in the material’s hardness.
Durometer Uses and Applications
Various industries use durometers to assure material quality and performance. You can use different types of durometers for different materials and applications, including pocket-sized models for field testing and bench-mounted versions for lab environments.
Advanced digital durometers can store data and provide more precise readings, enhancing quality control processes.
Here’s a closer look at durometer applications in measuring the hardness of rubber, elastomers, and plastics.
- Measuring Rubber Hardness: Hardness is a critical parameter in the rubber industry. Tire manufacturers rely on durometers to assess the hardness of different rubber compounds to ensure they meet safety and performance standards. Similarly, manufacturers of seals and gaskets use durometers to ensure their products have the necessary hardness to create effective seals under pressure.
- Assessing Elastomer Properties: Elastomers require precise hardness measurements to perform correctly in applications like automotive parts and medical devices. Durometers help manufacturers maintain consistent quality and functionality, ensuring that elastomer components are neither too soft (which could lead to deformation and failure) nor too hard (which could cause brittleness and cracking).
- Evaluating Plastic Hardness: Hardness can influence everything from durability to machining properties in plastics. Engineers and product designers use durometers to select appropriate materials for specific applications, like automotive parts and packaging.
What is a Durometer Part 3: Usage Tips
To get the most accurate and reliable results from your durometer, perform measurements in a controlled environment to minimize the effects of temperature and humidity on material hardness. Ensure the material’s surface is smooth and free from contaminants, as irregularities can affect the reading.
Handle the durometer carefully, avoiding drops or impacts that could misalign the calibration. Finally, regularly calibrate your durometer using standard reference materials to maintain accuracy.
Contact Us at I.B. Moore Company, LLC, for a Quote on Your Next Project
Discover top-quality industrial products at I.B. Moore Company, LLC. Our expert team provides tailored solutions for all your material needs. We offer reliable, durable, and precise rubber components to elevate your projects to the next level. Contact us in Lexington, Kentucky, for nationwide service.